【9回】インクジェットの真髄
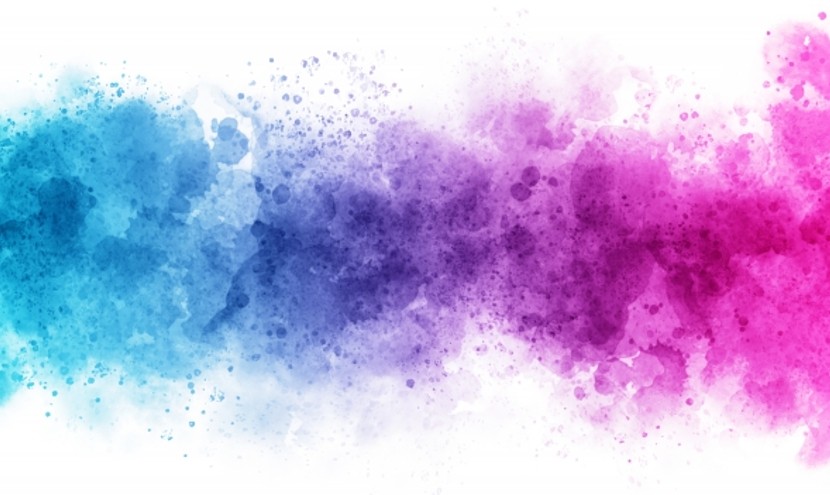
近年、インクジェット・プリンタの高画質化には目を見張るものがあります。
フィルムからの焼き付け(いわゆる従来の写真)と遜色の無い仕上がりとなることから、「写真」は、自分でプリントするのが普通のことになりつつあります。
そのインクジェット・プリントの最大の特徴と言えるのが、インクを微細なドロップ(水滴)として吹きつけ、文字や図柄、色を表現すること。
写真、版を直接押し付けてインクを転写する印刷とも、描画の原理は大きく異なっています。
特徴的であるとは、そこに技術の集約があることを意味します。
今回は、そうしたインクジェット・プリンタの技術を、レオロジーの視点から見ていきます。
インクを飛ばすことの難しさ
インクジェットのプリントでは、吹きつけられた微細なインク滴が1つの点(ドット)となり、その点が連続したり集積して面を構成することで、文字やグラフィックを媒体(紙)の上に表現しています。
そもそも高精度なプリントとは、オリジナルの画像をきちんと再現し得たもの。
そのためにはまず、インク滴が所定の着地点に正確に飛んでいく必要があります。
これは単純な線画を思い浮かべると分かり易いでしょう。
輪郭を構成する線、この線はドットの連続ですから、インク滴(ドット)が微妙にずれて着地したのでは、線が途切れたりガタガタになりますね。
そうならないよう、インク滴を狙い通りに飛ばす工夫がまず大事になります。
一方、美しいプリントを作るためにはインクの高機能化も重要です。
インク滴の正確な吐出技術、そしてインクの性能を決める成分構成の作り込み。
この二つの最適なコントロールが、インクジェット技術最大の急所と言えます。
プリント品質の中でも、シャープさ、階調性といったものはドットの大きさに関係しています。
プリンタ画像の精細さを示すのには解像度という基準が使われます。
単位はdpiで、これは1インチ当たりに入るドット数を表しています。
日本の大手プリンタ・メーカでは、スタンダードモデルでも4,800dpi(つまり1インチに4,800ドット)というスペックを持っており、この時1ドットを形成するインク滴の量は2ピコリットル(1plは1兆分の1リットル)なのだそうです。
ハイスペックモデルになると解像度は2倍の9,600dpi! 単位当たりのドット数が2倍になるのですから、当然、インク滴は半分の1ピコリットルです。
こうなると描画品質は格段に向上しますが、一方で余りに微小化すると、必要な位置に向けインク滴を正確に飛ばすことは難しくなっていきます。
特に、もともとサイズの大きい(・・・といってもナノメートル=10億分の1メートル単位ですが!)顔料粒子では、解像度が上がるに従って対応が難しくなります。
そのため家庭用プリンタでは、カラーは染料インク、くっきりとしたラインを描くためにブラックは顔料インクという構成が多くなっています。
顔料の分散安定技術
次にインクの工夫を見ましょう。
「写真」と品質を競うためには、発色が良い、耐水性・耐光性などに優れるといったインク特性が求められます。
顔料インクを例にしましょう。
顔料インクは、粒子サイズの色材が溶けずに溶媒に存在するものです。
紙繊維に染み込まず表面に固着して発色するため、滲みや退色が少なく、くっきり描ける特徴があります。
しかしこの粒子構造は欠点にもなります。ナノメートルという微小な粒子であっても、そのままではインクタンクの中で沈降してしまいます。
粒子同士がくっつき合えば、その傾向はなおさら進みます。
溶媒と色材が極端に言えば分離しているわけですから、上澄み部分が吐出されてしまうと色は着きません。
それではインクではありませんね。
さらには、吐出ノズルでの目詰まりという問題も起きてきます。
そこで顔料インクを使うためには、顔料粒子を細かくし、溶剤に均一に分散している(沈降しない)状態を作りだすことが必要となります。
これを顔料分散技術と言い、インクジェット・プリンタの品質を決める重要な技術となっています。
水性のインクジェット用インクではその8割程度が水で占められていますが、そこに水溶性でない顔料を分散させるためには、分散剤の添加が必要になります。
顔料によってその大きさや親水性は異なりますから、開発するインクごとに最適な添加剤の量を決めていかねばなりません。
分散剤の添加によって、溶媒である水は粘度を増すことになります。
つまり、分散剤を添加したインクの特性をつかむのに、粘度計測値が活用できることになります。
インクの品質 - 粘度との関係
適正な粘度を確保することは、微細なインク滴の安定した吐出にもつながります。
粘度が高まるにつれ、ノズルを通過する際の摩擦力は増大し吐出スピードが低下します。
結果、吐出量やサテライト(本滴の後ろにできる微小滴)の形状が不均一になり、印刷品質が落ちてしまいます。
例えば、大きなサテライトが媒体(紙)に着くと、シミや輪郭が滲んでいるように見えてしまいます。
違う色のインク滴(ドット)で比較するとさらに理解しやすいかもしれません。
プリントでは限られた色--赤(マゼンタ)、青(シアン)、イエローが最小単位--のドットを使って様々な色を表現しています。
例えば赤と青のドット数を規定の割合で使うことで紫色を作ります(正確には、紫に見える)。
この時、色は違ってもドットの大きさが一定であることが前提です。
それぞれの色のドット数が規定数であっても、ドットの大きさが違っていたのでは予定した色になりません。
これはインク滴の着地点がズレてしまっても同じです。
つまり、インクの吐出では、指示位置へまっすぐに飛ばすこと、余分なサテライトを形成しないことが重要と言えます。
そのためには、インク滴ができるだけ真球状になるよう設定するのが望ましいのですが、分散剤の添加により粘度の増加、他方で界面活性作用によって水(総体としてのインク)の表面張力が低下すると扁平した球になっていきます。
では粘度を極力下げれば解決かと言うと、今度は顔料粒子の分散安定性が低下してしまうのです。
どちらに転んでも不具合につながるこの状況をどうバランスさせるか?
インクメーカではその手段の1つとしてレオロジー特性を活用して理想値を探り、高品質なインクの研究開発、あるいは品質管理を行っているのです。
限りなく水に近い低粘性の物質を正確に計測するためには、やはり専門の技術とノウハウが必要です。
東機産業では、粘度計測機器を扱う日本のパイオニア企業としてさまざまなサポートをご提供し、優れたインクジェット用インクを生み出していくことに貢献しています。
インクジェット用インクの粘度測定は、円錐平板型(コーン・プレート型)回転粘度計が適しております。
一般的に分散安定性の評価には、低ずり速度(低回転速度)、ノズル吐出挙動の評価には、高いずり速度(高回転速度)での粘度値が用いられております。